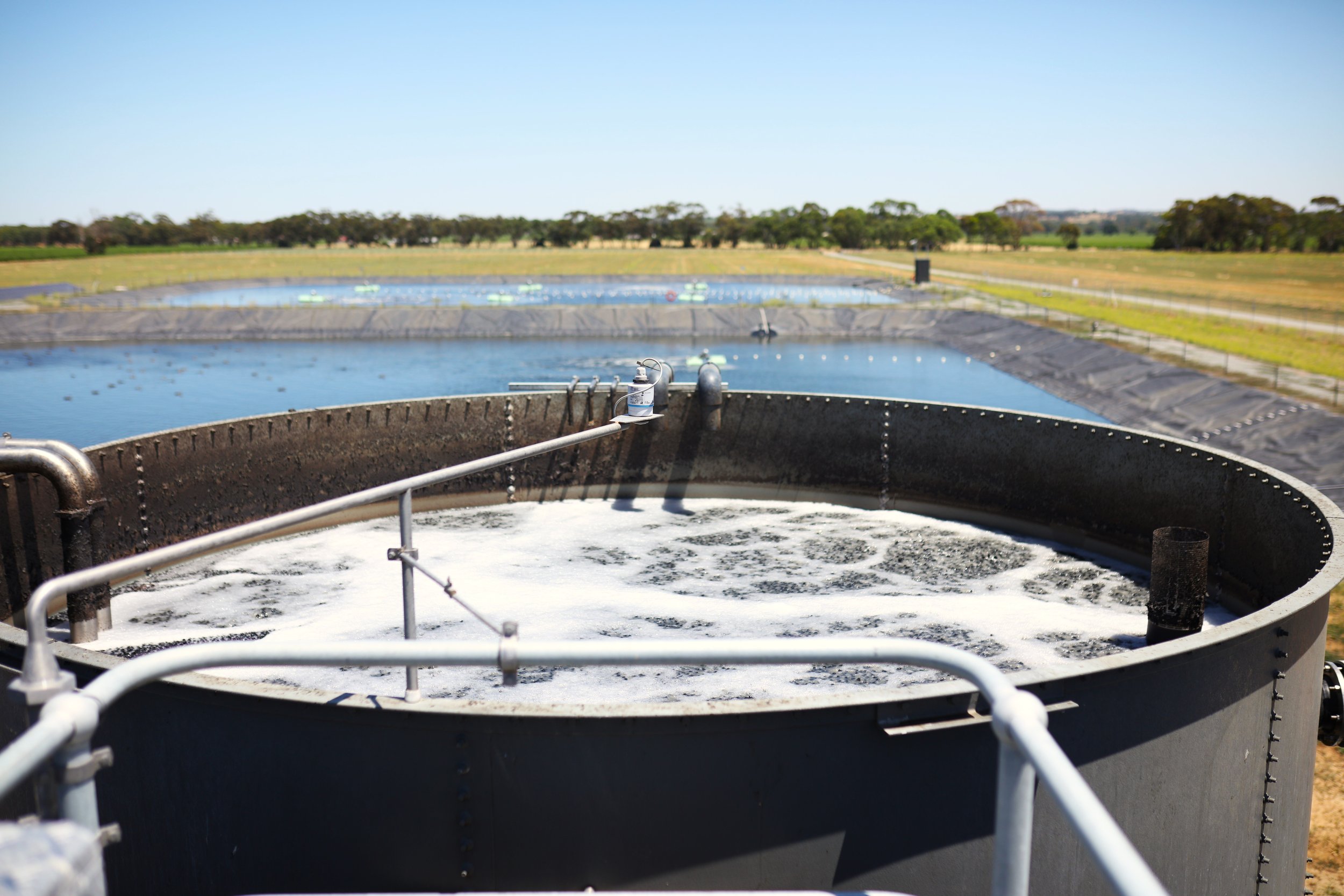
Frequently Asked Questions about MBBR
For Meat Processors, Food & Beverage Processors and Rendering Sites
Contents
Section 1: What is MBBR and how does it work?
Explanation of MBBR technology and its biological wastewater treatment process.
Overview of suspended carrier media and the formation of biofilm.
Section 2: Why Choose MBBR for Food and Beverage Processing Plants?
Discussion on the advantages of MBBR in the industry.
Cost-effectiveness, flexibility, scalability, and enhanced nutrient removal.
Section 3: What are the Design and Sizing Considerations for MBBR Systems?
Explanation of key factors to consider when designing and sizing MBBR systems.
Determining biofilm carrier volume and recommended ratios.
Hydraulic retention time (HRT) and its importance.
Oxygen supply and aeration considerations.
Section 4: How Do I Maintain and Optimise my MBBR System?
Explanation of key factors to consider when designing and sizing MBBR systems.
Determining biofilm carrier volume and recommended ratios.
Hydraulic retention time (HRT) and its importance.
Oxygen supply and aeration considerations.
Section 5: Waterform's Expertise in MBBR Solutions for Food and Beverage Processing Plants
Highlighting Waterform's experience in delivering ultraBiox MBBR solutions.
Showcase their expertise and successful projects in the industry.
Conclusion
MBBR FAQs
Section 1: What is MBBR and How Does it Work?
MBBR, short for Moving Bed Biofilm Reactor, is a biological wastewater treatment process widely used in food and beverage processing plants.
This innovative technology utilizes a suspended carrier media where microorganisms form a biofilm that effectively treats organic pollutants. The process involves the continuous movement of these carriers, providing a large surface area for the microorganisms to grow and thrive.
Key Benchmarks:
MBBR can achieve high removal rates of organic matter, typically exceeding 90%.
The technology is effective in reducing total suspended solids (TSS) and biological oxygen demand (BOD), meeting stringent environmental regulations.
Section 2: Why Choose MBBR for Food and Beverage Processing Plants?
MBBR offers numerous advantages that make it an excellent choice for wastewater treatment in the food and beverage industry.
It’s comparatively cost-effective.
MBBR can be a cost-effective option due to its simplicity and low energy requirements. Compared to traditional treatment methods, MBBR systems generally have lower capital and operational costs.
Flexibility and Scalability.
MBBR systems are modular and easily scalable, allowing for future expansions as your processing plant grows. The flexibility of MBBR technology enables efficient management of varying wastewater loads and composition.
Enhanced Nutrient Removal.
In addition to organic matter, MBBR can also facilitate the removal of nutrients like nitrogen and phosphorus. This feature is particularly beneficial for meeting regulatory standards and minimizing environmental impact.
Section 3: What are the Design and Sizing Considerations for MBBR Systems?
To ensure optimal performance, proper design and sizing of MBBR systems are crucial. Here are some essential considerations:
Determining Biofilm Carrier Volume
The carrier volume is a key parameter that influences the treatment capacity of the MBBR system. As a general guideline, a carrier-to-wastewater ratio of 40-70% is recommended, depending on the specific process requirements.
Hydraulic Retention Time (HRT)
HRT refers to the average duration that wastewater spends in the MBBR system. Typically, a HRT of 4-8 hours is suitable for food and beverage processing plants, but this can vary depending on the specific industry and regulatory requirements.
Oxygen Supply
Adequate oxygen supply is essential for the growth and activity of the microorganisms. Ensure proper aeration and consider using energy-efficient solutions like fine bubble diffusers to maintain optimal dissolved oxygen levels.
Section 4: How Do I Maintain and Optimise my MBBR System?
Regular maintenance and optimization are vital to maximize the performance and longevity of MBBR systems. Consider the following tips:
Monitoring and Sampling
Implement a monitoring program to assess the system's performance regularly. Regular sampling and testing of influent and effluent parameters will help identify any deviations and enable prompt corrective actions.
Sludge Management
Monitor the sludge blanket regularly to prevent excessive accumulation and potential process upsets. Consider implementing a sludge wasting strategy to maintain a healthy biomass concentration within the MBBR.
Proper Load Management
Avoid sudden spikes in wastewater flow or composition, as this can negatively impact the MBBR's performance. Implement proper load management practices, such as equalization tanks or flow balancing, to ensure stable operation.
Section 5: Waterform's Expertise in MBBR Solutions for Food and Beverage Processing Plants
When it comes to selecting an MBBR solution for your food and beverage processing site, it's essential to partner with experienced providers like Waterform.
With their expertise in delivering ultraBiox MBBR solutions, Waterform has a proven track record in designing and implementing efficient wastewater treatment systems tailored to the industry's needs.
Conclusion
In this article, we have explored the frequently asked questions about MBBR technology in food and beverage processing plants.
We have discussed the working principles of MBBR, its advantages, design considerations, maintenance tips, and highlighted Waterform's experience in delivering MBBR solutions.
By leveraging MBBR technology, you can achieve efficient and cost-effective wastewater treatment, ensuring compliance with regulations while minimizing your environmental footprint.
Remember to analyse your specific site requirements and consult with industry experts to design an optimal MBBR system that meets your needs.
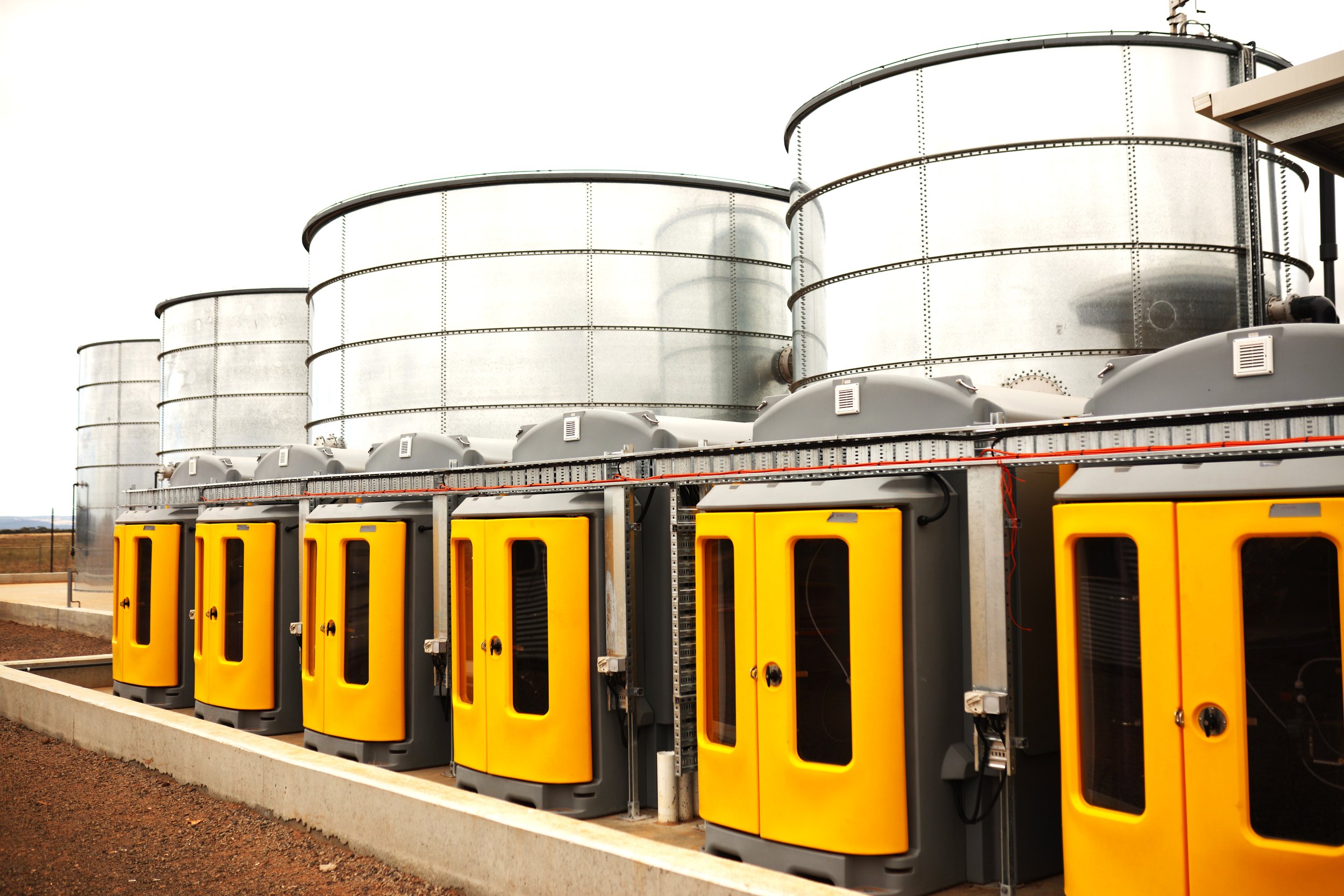