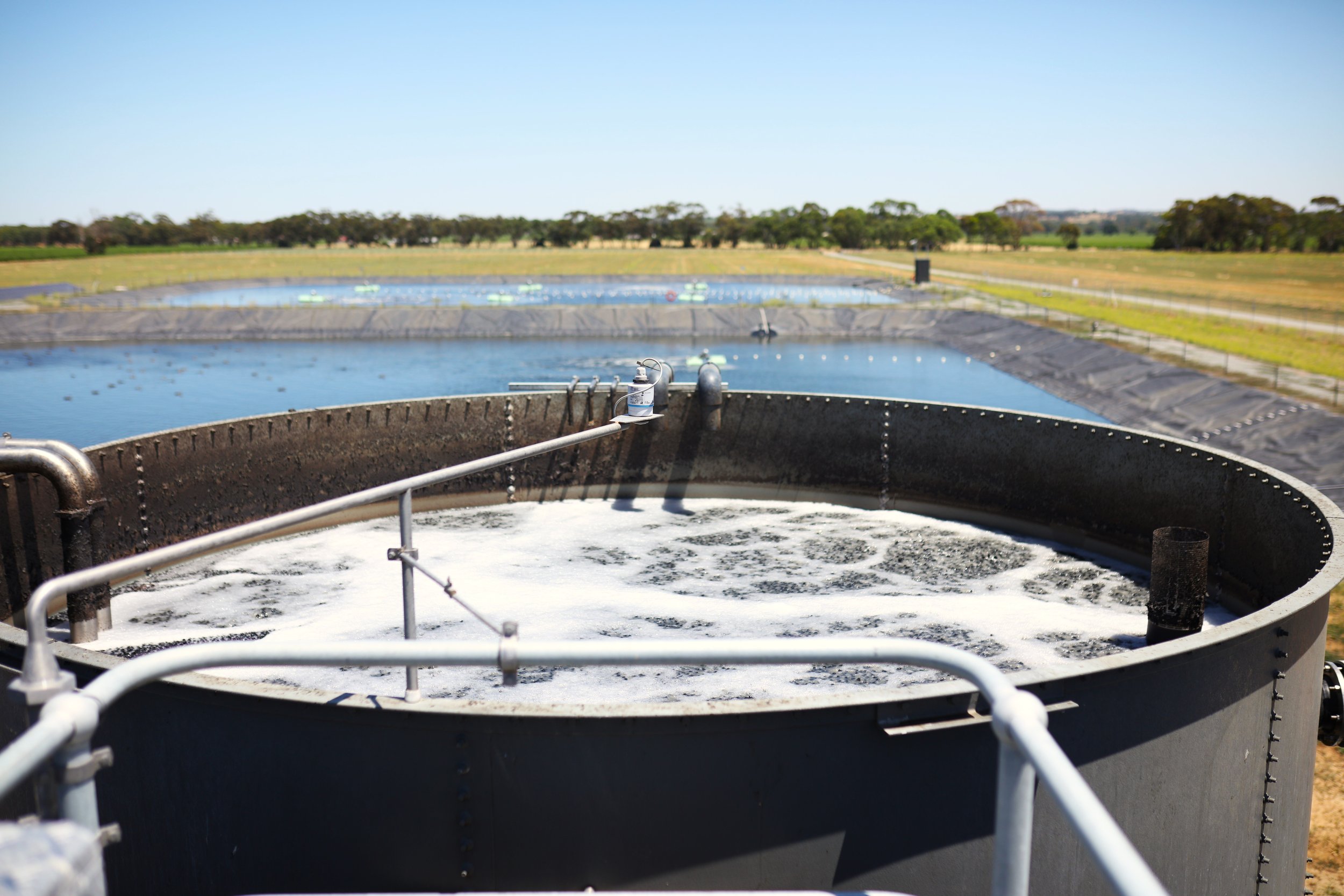
Cost of an MBBR System for Food and Beverage Processing Plants
For Meat Processors, Food & Beverage Processors and Rendering Sites
Contents
Section 1: Understanding MBBR Systems
Section 2: Factors Influencing MBBR System Costs
2.1 Treatment Capacity
2.2 Site-Specific Requirements
2.3 Equipment and Technology
2.4 Installation and Construction
Section 3: Cost Breakdown for MBBR Systems
3.1 Equipment Costs
3.2 Design and Engineering Costs
3.3 Installation and Construction Costs
3.4 Permitting and Compliance Costs
Section 4: Benchmark Costs and Tips
4.1 Small-Scale MBBR System
4.2 Medium-Scale MBBR System
4.3 Large-Scale MBBR System
Conclusion
Welcome to the comprehensive guide on the cost of an MBBR (Moving Bed Biofilm Reactor) system for food and beverage processing plants.
As a food or beverage processor, you understand the importance of wastewater treatment to maintain environmental compliance and sustainable practices.
However, one crucial factor that often influences your decision-making process is cost.
In this article, we will delve into the detailed analysis of the costs involved in setting up an MBBR system specifically designed for small, medium, and large meat processing plants. We will provide practical insights, benchmarks, and formulas to help you make informed decisions.
Section 1: Understanding MBBR Systems
Before we dive into the cost analysis, let's briefly understand what an MBBR system entails and why it is a popular choice for food and beverage processing plants.
MBBR is a biological wastewater treatment technology that utilizes a suspended biofilm to remove organic pollutants from wastewater.
This highly efficient system offers advantages such as compact design, flexibility, and ease of operation.
Section 2: Factors Influencing MBBR System Costs
2.1. Treatment Capacity
The size and capacity of the MBBR system are major cost determinants.
Smaller processing plants typically require systems with a lower treatment capacity, while larger facilities necessitate more extensive and advanced systems.
Determining your processing plant's average wastewater flow and pollutant load will help you estimate the appropriate treatment capacity and associated costs.
2.2. Site-Specific Requirements
Every food and beverage processing site has unique requirements and challenges.
Factors like space availability, environmental regulations, discharge standards, and the need for additional pre-treatment or post-treatment processes influence the overall system design and cost.
Consulting with experienced professionals like Waterform, who have expertise in delivering MBBR solutions, can help you assess these site-specific factors effectively.
2.3. Equipment and Technology
The choice of equipment and technology used in the MBBR system significantly impacts the cost.
Considerations include the quality and durability of components, automation and control systems, energy efficiency, and the integration of advanced features like remote monitoring and data analytics. Evaluating different options and their long-term benefits will help you strike the right balance between cost and performance.
2.4. Installation and Construction
The complexity of installation and construction also affects the overall cost. Factors such as site preparation, excavation, foundation requirements, piping, electrical connections, and ancillary infrastructure should be considered.
Collaborating with an experienced contractor or system provider, like Waterform, ensures efficient installation while minimizing any unexpected expenses.
Section 3: Cost Breakdown for MBBR Systems
3.1. Equipment Costs
The equipment costs typically constitute a significant portion of the total MBBR system cost.
These include biofilm carriers, aeration devices, blowers, diffusers, tanks, and other required components. Waterform's experience in delivering ultraBiox MBBR solutions for food and beverage processing sites ensures quality equipment tailored to industry needs.
Approximately 40-50% of the total capital cost is allocated to equipment expenses.
This includes biofilm carriers, aeration devices, blowers, diffusers, tanks, and other necessary components. It is crucial to invest in high-quality equipment to ensure long-term performance and reliability.
3.2. Design and Engineering Costs
Design and engineering costs involve the planning, system layout, and process design. These costs cover the development of detailed engineering drawings, hydraulic calculations, and equipment specifications.
Collaborating with knowledgeable professionals during this stage ensures an optimal design that meets regulatory requirements and maximizes operational efficiency.
Design and engineering expenses typically account for around 10-15% of the total capital cost.
These costs cover the planning, system layout, process design, engineering drawings, hydraulic calculations, and equipment specifications. Collaborating with knowledgeable professionals during this stage ensures an optimized design that meets regulatory requirements and maximizes operational efficiency.
3.3. Installation and Construction Costs
Installation and construction costs encompass site preparation, civil works, equipment installation, electrical connections, and commissioning.
Professional installation services provided by Waterform help ensure a seamless and efficient setup, reducing potential delays and cost overruns.
Installation and construction expenses generally make up about 20-30% of the total capital cost.
These costs encompass site preparation, civil works, equipment installation, electrical connections, and commissioning. Engaging experienced contractors or system providers can help ensure a smooth and efficient installation process, minimizing potential delays and cost overruns.
3.4. Permitting and Compliance Costs
Obtaining necessary permits, licenses, and complying with environmental regulations can incur costs. It is essential to consider fees associated with environmental impact assessments, discharge permits, and ongoing compliance monitoring.
Proactively engaging with local regulatory bodies will help you accurately estimate these costs.
Permitting and compliance costs typically represent around 5-10% of the total capital cost.
These expenses include obtaining necessary permits, licenses, conducting environmental impact assessments, and complying with regulatory requirements. It is important to allocate budget for fees associated with environmental impact assessments, discharge permits, and ongoing compliance monitoring.
Section 4: Benchmark Costs and Tips
4.1. Small-Scale MBBR System
As an example, for small meat processing plants with a wastewater flow rate of around 50-100 kilolitres per day (kL/day), the capital cost of an MBBR system (including associated pre-treatment and post-treatment, installation and site works) can range between $500,000 and $1,000,000 AUD.
It's important to focus on cost-effective equipment selection, efficient layout design, and leveraging available space optimally.
4.2. Medium-Scale MBBR System
Medium-sized food and beverage processing plants with wastewater flow rates of 100 kilolitres per day (kL/day) up to 1 megalitre per day (1ML/day) may require an MBBR system (including associated pre-treatment and post-treatment, installation and site works) with a capital cost ranging from $1,000,000 to $12,000,000 AUD.
4.3. Large-Scale MBBR System
For larger meat processing plants with higher wastewater flow rates exceeding 1 megalitre per day, the capital cost of an MBBR system (including associated pre-treatment and post-treatment, installation and site works) can exceed $12,000,000 AUD.
Efficient engineering design, advanced automation, and scalability considerations become crucial at this scale.
Conclusion
Investing in an MBBR system for your food and beverage processing plant is a critical step towards sustainable wastewater management.
By understanding the factors influencing the cost and breaking down the cost components, you can make informed decisions tailored to your specific needs.
Remember to consider treatment capacity, site-specific requirements, equipment and technology, and installation and construction aspects. Collaborating with experienced system providers, such as Waterform, ensures reliable solutions and expert guidance throughout the process.
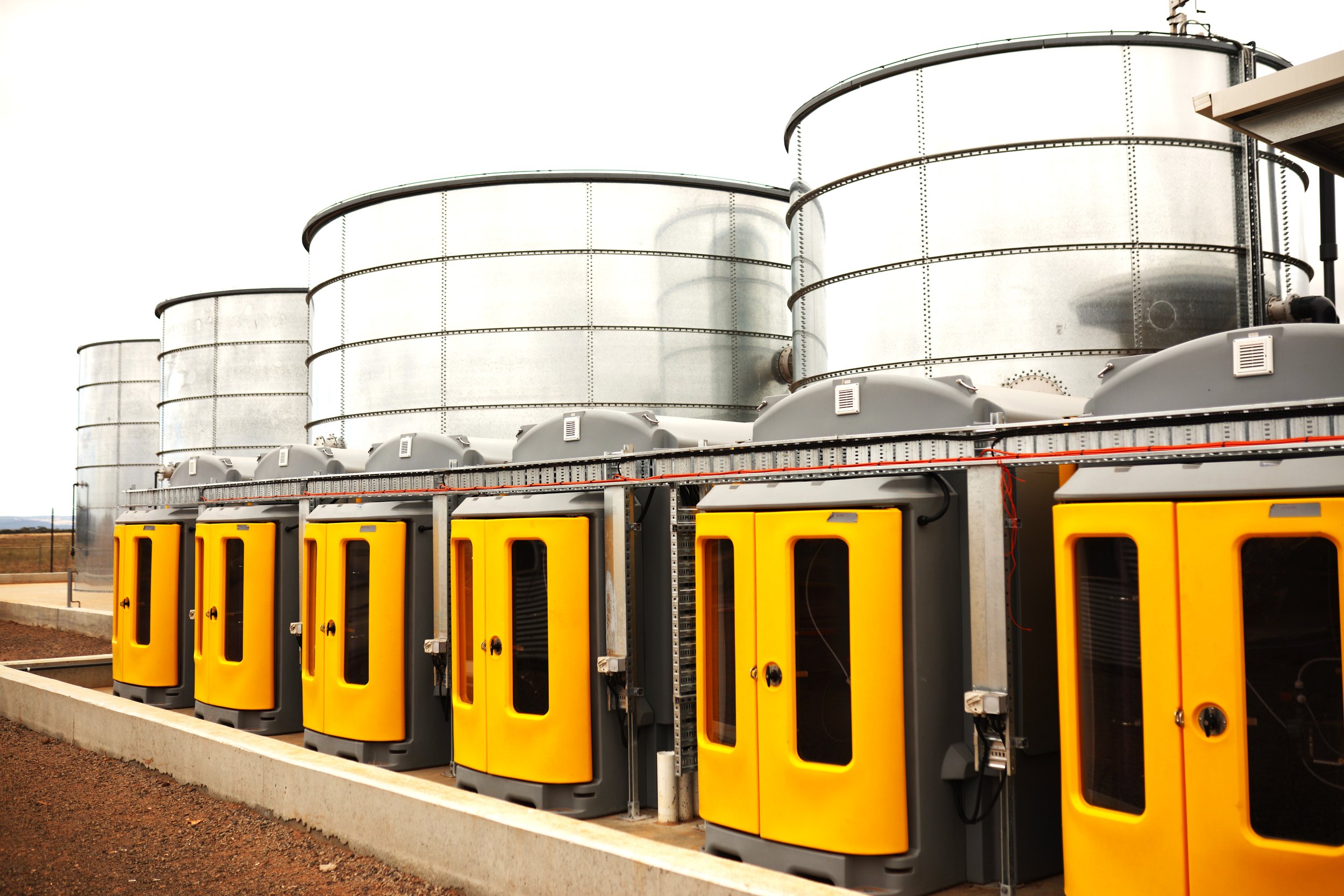